Level switches are simple devices. They tell you when liquid or solid materials reach a certain point in a tank. These switches are very important in factories and plants.
Many companies use level switches every day. They help keep workers safe. They also protect expensive equipment from damage.
Level switches work like alarm systems. When the material gets too high or too low, they send a signal. This signal can turn pumps on or off. It can also sound alarms.
These devices are much simpler than other measuring tools. They just say “yes” or “no” about the level. They don’t give exact measurements like rulers do.
How Do Level Switches Work?
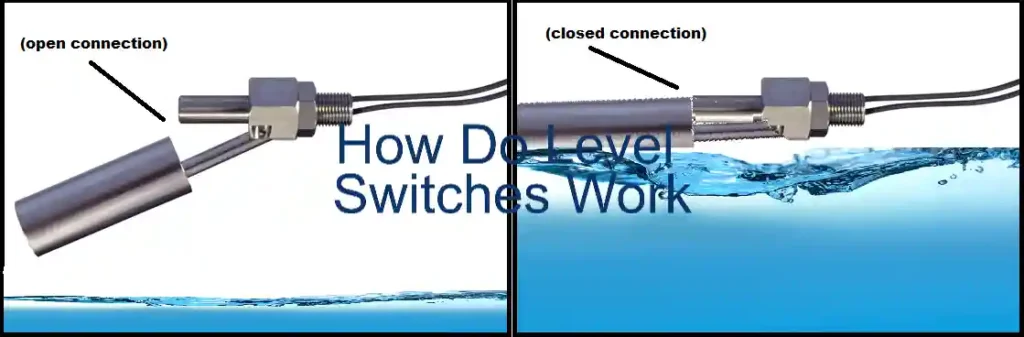
Level switches use different methods to detect materials. Each method works in its own way. Here are the main ways they work:
- They float on top of liquids
- They feel the weight of materials
- They use electricity to sense liquids
- They send out sound waves
- They use light beams
- They shake and feel when materials touch them
The basic process is always the same. First, the switch detects a change. Then it sends an electrical signal. Finally, other equipment responds to this signal.
Most level switches are very simple inside. They have few moving parts. This makes them last longer and break less often.
Main Types of Level Switches
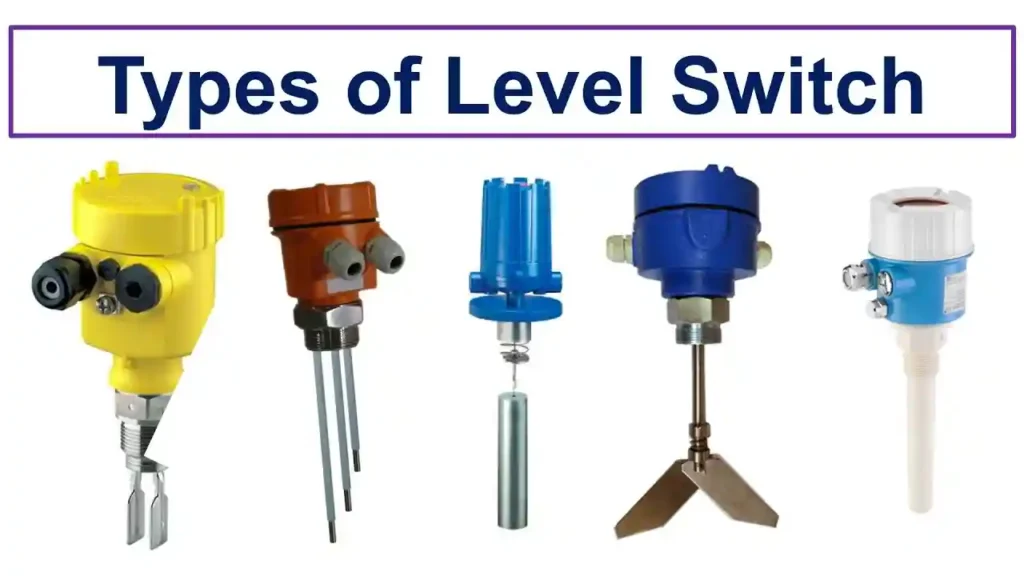
There are many different types of level switches. Each type works best for certain jobs. Let’s look at the most common ones.
Float Level Switches
Float level switches are the most popular type. They work like fishing bobbers on water.
How Float Switches Work
- A plastic or metal ball floats on the liquid
- The ball goes up when liquid level rises
- The ball goes down when liquid level drops
- Inside the ball is a magnet
- The magnet turns the switch on or off
Good Points of Float Switches
- They are very simple to understand
- They don’t need electricity to work
- They cost less money than other types
- They work with most liquids
- They last a long time
Bad Points of Float Switches
- The floating part can get stuck
- Dirty liquids can make them stop working
- They only work with liquids, not powders
- They need space to move up and down
- Strong chemicals can damage them
Where People Use Float Switches
- Water tanks in buildings
- Swimming pools
- Fuel tanks in cars
- Chemical storage tanks
- Fish tanks and ponds
Magnetic Level Switches
Magnetic level switches are similar to float switches. But they work better in tough conditions.
How They Work
- They use magnets to turn switches on and off
- The magnet part never touches the liquid
- This keeps the electrical parts clean and safe
- They can work in very hot or cold places
Why People Like Them
- They never need repairs
- They work for many years
- They are safe around dangerous chemicals
- They can handle high pressure
- They work in places where explosions might happen
Electronic Level Switches
Electronic level switches don’t have moving parts. This makes them very reliable.
Capacitive Level Switches
- They feel changes in electrical fields
- They work with both liquids and powders
- You can adjust how sensitive they are
- Foam and bubbles don’t confuse them
Ultrasonic Level Switches
- They use sound waves like bats do
- They don’t touch the material at all
- They work with dangerous chemicals
- They clean themselves
Optical Level Switches
- They use light beams to detect materials
- They are very accurate
- They work well with clear liquids
- They are very small
Conductive Level Switches
These switches work only with liquids that conduct electricity. Water is a good example.
How They Work
- They have metal probes that go into the liquid
- When liquid touches both probes, electricity flows
- This flow turns the switch on
- They are very simple and cheap
Where They Work Best
- Water treatment plants
- Cooling towers
- Steam boilers
- Fish farms
Thermal Level Switches
Thermal switches use heat to detect materials.
How They Work
- They have a small heater inside
- The heater stays hot when surrounded by air
- When material covers the heater, it cools down
- The switch detects this temperature change
Good Things About Them
- No moving parts to break
- They work with sticky materials
- They work with both liquids and powders
- The heat helps keep them clean
Vibrating Level Switches
These switches shake back and forth like tuning forks.
How They Work
- A small motor makes a metal fork vibrate
- The vibration changes when material touches the fork
- The switch detects this change in vibration
- It then sends a signal
Why They’re Useful
- The shaking motion keeps them clean
- They work great with powders
- They are very sensitive
- They don’t take up much space
Rotating Paddle Level Switches
These switches have spinning paddles like boat propellers.
How They Work
- A small motor spins a paddle slowly
- When material piles up, the paddle gets stuck
- The motor works harder and draws more electricity
- The switch detects this extra electricity use
Best Uses
- Grain storage bins
- Cement silos
- Sand and gravel piles
- Coffee bean storage
Where People Use Level Switches
Level switches are used in many different industries. Each industry has special needs.
Water Treatment Plants
- Pump Control: Stop pumps from running dry
- Tank Management: Keep water at the right level
- Filter Systems: Know when to clean filters
- Chemical Addition: Add the right amount of treatment chemicals
Chemical Factories
- Safety Systems: Prevent dangerous overflows
- Storage Tanks: Track how much chemical is stored
- Mixing Processes: Add ingredients at the right time
- Waste Control: Monitor waste levels
Oil and Gas Companies
- Separator Tanks: Separate oil, water, and gas
- Storage Monitoring: Prevent spills and overflows
- Pipeline Safety: Detect leaks quickly
- Drilling Operations: Monitor drilling fluid levels
Food and Drink Companies
- Ingredient Storage: Know when to order more supplies
- Mixing Tanks: Control recipe ingredients
- Cleaning Systems: Monitor cleaning solution levels
- Product Storage: Track finished products
Medicine Companies
- Clean Rooms: Keep sterile conditions
- Batch Making: Ensure consistent quality
- Solvent Recovery: Reuse expensive solvents
- Quality Control: Monitor testing materials
Heating and Cooling Systems
- Water Drainage: Prevent overflow damage
- Cooling Towers: Maintain proper water levels
- Boiler Safety: Prevent dangerous conditions
- Chiller Systems: Monitor coolant levels
Mining Companies
- Waste Management: Monitor waste piles
- Water Control: Manage water usage
- Material Transport: Control conveyor systems
- Dust Control: Maintain water for dust suppression
How to Install Level Switches
Good installation is very important. Poor installation causes most problems.
Before You Start
- Study Your Application: Know what material you’re measuring
- Check Conditions: Look at temperature, pressure, and chemicals
- Plan Electrical Work: Make sure you have the right power
- Think About Access: Plan for future maintenance
Installation Steps
Physical Installation
- Choose Location: Pick the right spot for the switch
- Mount Securely: Make sure it won’t vibrate loose
- Allow Movement: Give float switches room to move
- Protect from Weather: Use proper covers outdoors
Electrical Connection
- Use Right Cables: Choose cables that resist chemicals
- Ground Properly: Connect safety grounds correctly
- Protect from Surges: Install surge protectors
- Test Connections: Check all wires before starting
Testing Your Installation
- Check Settings: Make sure all adjustments are correct
- Test Operation: Fill and empty the tank to test switching
- Test Alarms: Make sure warning systems work
- Keep Records: Write down all settings and test results
Good Things About Level Switches
Level switches offer many benefits for businesses and workers.
Safety Benefits
- Prevent Accidents: Stop dangerous overflows before they happen
- Protect Workers: Keep people away from dangerous areas
- Equipment Protection: Save expensive pumps and motors
- Environmental Safety: Prevent spills and contamination
Money Benefits
- Low Cost: Cheaper than complex measuring systems
- Long Life: Work for many years without replacement
- Save Energy: Run pumps only when needed
- Reduce Labor: Less manual checking required
Technical Benefits
- Simple Operation: Easy to understand and use
- Fast Response: React quickly to level changes
- Reliable: Work consistently day after day
- Easy Integration: Connect easily to existing systems
Problems with Level Switches
Level switches also have some limitations you should know about.
Technical Problems
- Limited Information: Only tell you “high” or “low”
- Single Point: Each switch watches only one level
- Environmental Effects: Heat and cold can affect some types
- Calibration Needs: Need adjustment over time
Application Limits
- Chemical Limits: Some chemicals can damage switches
- Installation Needs: May require cutting holes in tanks
- Access Problems: Hard to reach for maintenance
- Power Needs: Electronic types need reliable electricity
Cost Issues
- Multiple Switches: Need separate switches for multiple levels
- Special Types: Some applications need expensive switches
- Installation Cost: May need professional installation
- Maintenance Cost: Regular checking and adjustment needed
How to Choose the Right Level Switch
Picking the right switch depends on many factors. Here’s what to consider.
Your Application Needs
- Material Type: Liquid or powder, thick or thin
- Operating Conditions: Hot, cold, high pressure, or vacuum
- Number of Switch Points: How many levels you need to monitor
- Speed Requirements: How fast the switch must respond
Environmental Factors
- Temperature: How hot or cold it gets
- Pressure: Normal, high, or vacuum conditions
- Chemical Safety: What chemicals the switch will touch
- Explosion Risk: Special switches for dangerous areas
Performance Needs
- Accuracy: How precise the switching point must be
- Switching Difference: Gap between on and off points
- Output Type: What kind of signal you need
- Power Available: Voltage and current available
Installation Factors
- Mounting Method: How to attach the switch
- Size Limits: How much space you have
- Wire Connections: What kind of electrical connections
- Maintenance Access: How easy it is to service
Taking Care of Level Switches
Regular care keeps level switches working properly for many years.
Regular Maintenance
- Visual Checks: Look for damage or buildup
- Electrical Testing: Test wires and connections
- Movement Testing: Check that moving parts work freely
- Calibration Checks: Verify switching points are correct
Common Problems and Fixes
Float Switch Problems
- Stuck Float: Clean the float area and remove buildup
- Erratic Switching: Check for worn parts and replace them
- No Signal: Test electrical connections and switch contacts
Electronic Switch Problems
- Power Problems: Check that voltage and current are correct
- Interference: Make sure electrical grounding is good
- Drift: Recalibrate according to instructions
Troubleshooting Steps
- Safety First: Turn off power and follow safety rules
- Look First: Check for obvious problems
- Test Electrical: Use meters to check operation
- Test Function: Try the switch with known level changes
- Write Notes: Record what you find and what you fix
Future of Level Switch Technology
Level switch technology keeps getting better. Here are some new developments.
Smart Features
- Wireless Connection: Send signals without wires
- Predictive Maintenance: Warn before problems happen
- Digital Integration: Work better with computer systems
- Data Analysis: Use information to improve processes
Better Materials
- Chemical Resistance: Handle more aggressive chemicals
- Longer Life: Last longer before replacement
- Smaller Size: Fit in tighter spaces
- Eco-Friendly: Better for the environment
Improved Performance
- Higher Accuracy: More precise switching points
- Faster Response: React more quickly to changes
- Wider Temperature Range: Work in more extreme conditions
- Enhanced Safety: Additional safety features
Conclusion
Level switches are vital industrial tools that detect material levels in tanks and containers. Various types suit different applications, from basic float switches to advanced electronic models. Success requires careful selection based on specific needs, proper installation, and regular maintenance. These cost-effective devices improve safety, protect equipment, and boost efficiency. With advancing technology, level switches remain reliable solutions for critical monitoring needs across all industries.
