In the modern world competitive business landscape and other organizations finding ways to reduce production costs. By identifying areas of inefficiency, implementing cost-effective strategies and leveraging technology businesses can optimize their operations and increase profitability.
By performing effective cost reduction measures, can provide competitive advantages and contribute to the long-term success of any business. Any businesses organization can achieve sustainable cost reductions while maintaining product quality and customer satisfaction. Here are some tips for reducing business production costs:
Explore Alternative Suppliers and Materials
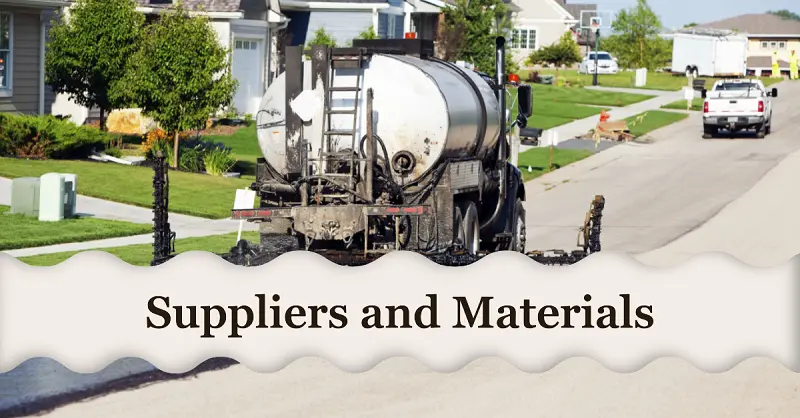
Exploring alternative suppliers and materials is a valuable strategy to reduce production costs and improve overall profitability. By considering different options businesses can find suppliers with competitive pricing, better quality and faster delivery times. Here are some points to consider when exploring alternative suppliers and materials:
1. Shop around and compare prices
Do complete market research to identify potential suppliers that offer competitive prices for the materials or inputs you require. Obtain quotes from multiple suppliers and compare them to determine the best value for your business. Remember to consider factors such as quality, reliability and customer service alongside pricing.
2. Evaluate supplier reputation and reliability
When considering alternative suppliers it is essential to assess their reputation and reliability. Look for suppliers with a proven track record of delivering on time and providing consistent quality. Online reviews, references from other businesses and industry networks can provide valuable insights into a supplier’s reliability.
3. Assess quality standards
Ensure that alternative suppliers meet your quality standards and specifications. Request samples or conduct product testing to verify the quality of materials before committing to a new supplier.
4. Consider delivery times and logistics
Timely delivery of materials is an important factor for efficient production. Evaluate the delivery capabilities and logistics of alternative suppliers. Determine first if they can meet your production schedule and if their shipping methods align with your requirements. Faster delivery times can lead to reduced inventory costs and improved operational efficiency.
5. Evaluate eco-friendly materials
Exploring eco-friendly materials can provide long-term benefits for your business. Sustainable materials may offer cost savings through reduced energy consumption, improved durability, or lower waste generation. Conduct research to identify environmentally friendly alternatives that align with your product requirements.
6. Negotiate favorable terms
By Engaging with alternative suppliers take the opportunity to negotiate favorable terms. Seek volume discounts, longer payment terms, or other incentives that can further reduce production costs. Building strong relationships with suppliers can lead to more favorable pricing and terms in the long run.
7. Pilot test and monitor performance
Before doing full committing to a new supplier consider piloting a small-scale production run or conducting a trial period. This allows you to evaluate their performance including quality, reliability, and the impact on overall production costs.
8. Maintain contingency plans
When exploring alternative suppliers and materials, it’s essential to have contingency plans in place. Unexpected disruptions or issues with the new supplier may occur, so it’s crucial to have backup options or alternative sourcing strategies to mitigate any potential risks to production.
Improve Inventory Management: Strategies for Efficient Operations
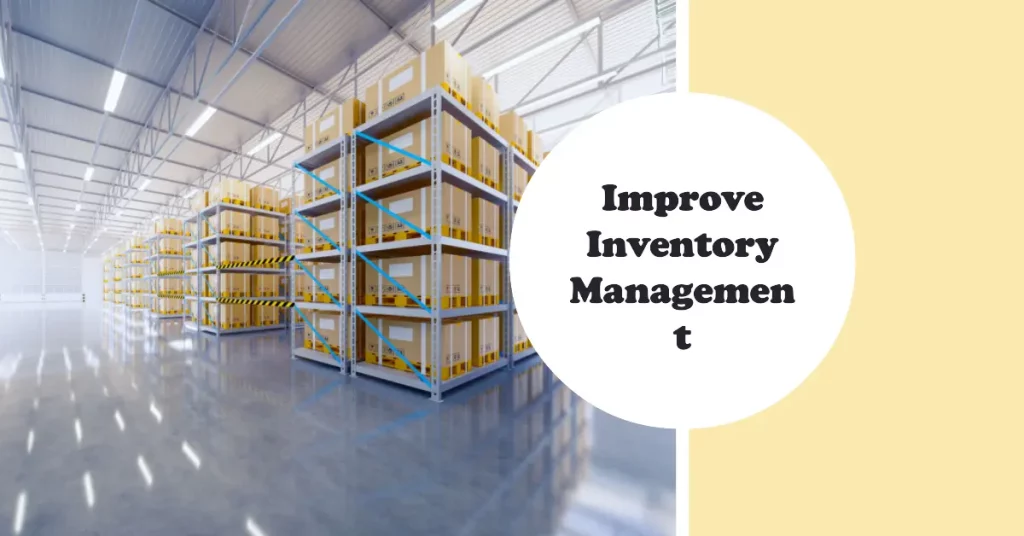
Efficient inventory management is crucial for businesses to minimize waste, reduce storage costs, and optimize overall operations. By implementing effective strategies, companies can ensure that their inventory levels align with customer demand while avoiding excess stock and stock outs. In this article, we will explore key strategies to improve inventory management and achieve efficient operations.
1. Implement Just-In-Time (JIT) Inventory Management
Just-In-Time (JIT) inventory management is a strategy that aims to minimize inventory levels by ordering and receiving products precisely when they are needed. By synchronizing the production and delivery of goods with customer demand, businesses can reduce the costs associated with excess inventory and storage space. JIT allows for a leaner and more agile supply chain, enabling companies to respond quickly to changing market demands.
2. Utilize Inventory Tracking and Management Software
Implementing inventory tracking and management software provides businesses with real-time visibility into their inventory levels, stock movements, and order status. These tools automate the process of monitoring inventory, tracking product lifecycles, and generating reports, enabling businesses to make data-driven decisions and optimize reordering strategies.
Inventory tracking software helps identify slow-moving items, prevent stock outs, and streamline the procurement process. By centralizing inventory data and integrating it with other business systems, companies can gain insights into customer demand patterns, lead times, and reorder points. This level of visibility and control allows businesses to optimize their inventory levels, reduce carrying costs, and improve overall operational efficiency.
3. Implement Effective Demand Planning
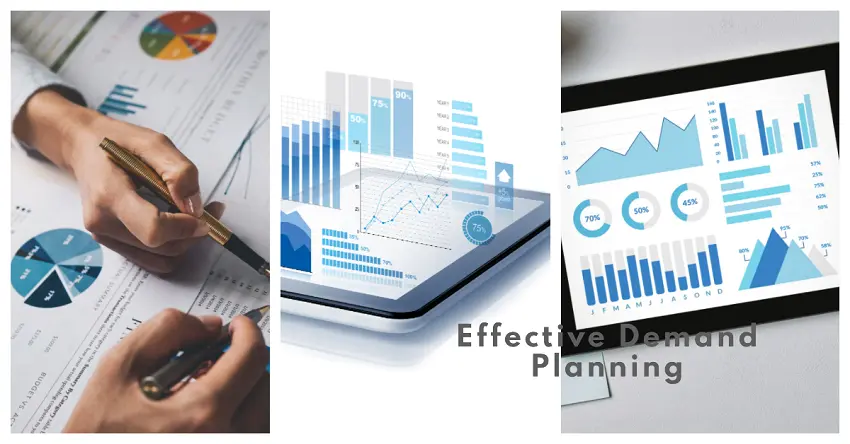
Accurate demand planning is essential for efficient inventory management. By analyzing historical sales data, market trends, and customer behavior, businesses can forecast demand more accurately and adjust their inventory levels accordingly. Effective demand planning helps prevent excess inventory, stock outs, and costly rush orders.
To enhance demand planning, businesses can utilize statistical forecasting models, collaborate with sales and marketing teams, and leverage customer feedback. By actively monitoring and adjusting demand forecasts, companies can align their inventory levels with market demand, improve order fulfillment rates, and reduce carrying costs.
4. Optimize Warehouse Layout and Organization
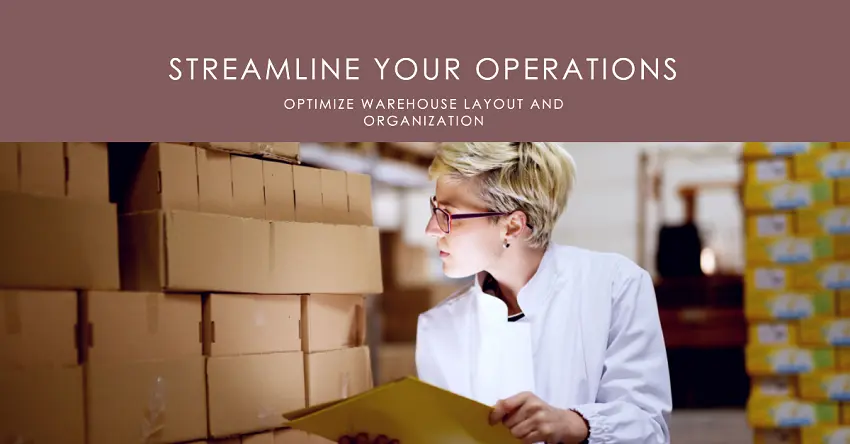
An organized and efficient warehouse layout plays a critical role in inventory management. By optimizing the physical arrangement of products, businesses can improve inventory visibility, reduce picking and storage times, and enhance overall productivity.
Strategic placement of fast-moving items near shipping areas and implementing effective labeling systems can streamline order fulfillment processes. Additionally, employing warehouse management systems (WMS) can automate inventory tracking, improve order accuracy, and optimize storage capacity.
5. Foster Collaboration with Suppliers and Partners
Collaborating closely with suppliers and partners can significantly improve inventory management. By establishing strong relationships, companies can enhance communication, streamline order processes, and negotiate favorable terms.
Maintaining open lines of communication with suppliers helps in aligning production schedules, managing lead times, and coordinating deliveries. Collaborative forecasting and planning initiatives allow businesses to share information and make joint decisions to optimize inventory levels and reduce costs throughout the supply chain.
Enhance Operational Efficiency: Strategies for Streamlining Processes
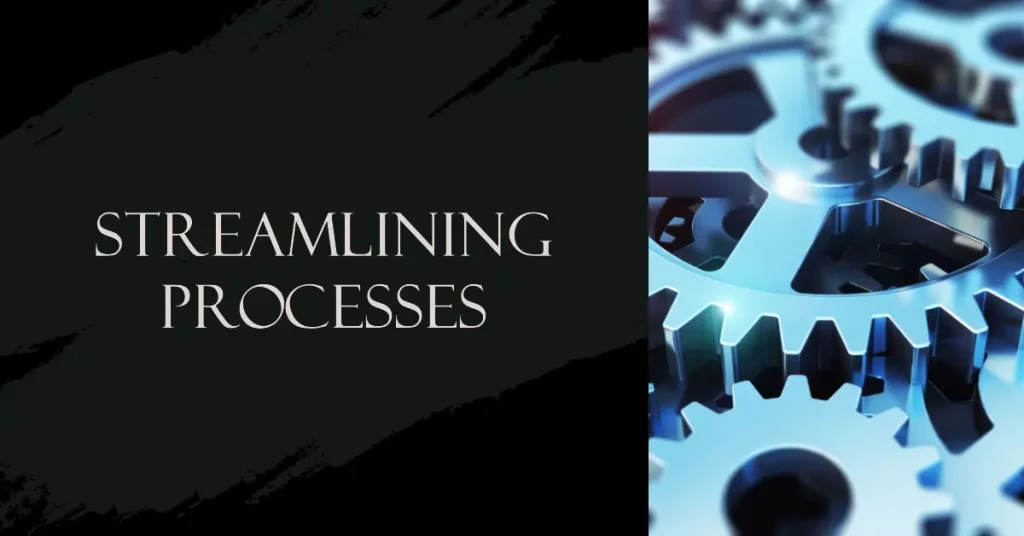
The enhancement in operational efficiency is necessary to reduce costs, improve productivity and stay competitive. By streamlining processes and optimizing resource allocation, companies can achieve higher output quality, minimize waste and maximize overall efficiency.
1. Implement Lean Manufacturing Techniques
Lean about manufacturing techniques are widely recognized for their ability to streamline processes and eliminate waste. By analyzing the production process and identifying non-value-added activities, businesses can optimize workflow, improve efficiency, and reduce costs.
Implementing practices such as Value Stream Mapping (VSM) helps the visualize and analyze the flow of materials and information throughout the production process. This allows identifying bottlenecks, unnecessary steps and areas of inefficiency. By eliminating waste, optimizing process flows, and standardizing procedures, companies can improve productivity, enhance quality and reduce costs.
2. Invest in Employee Training and Development
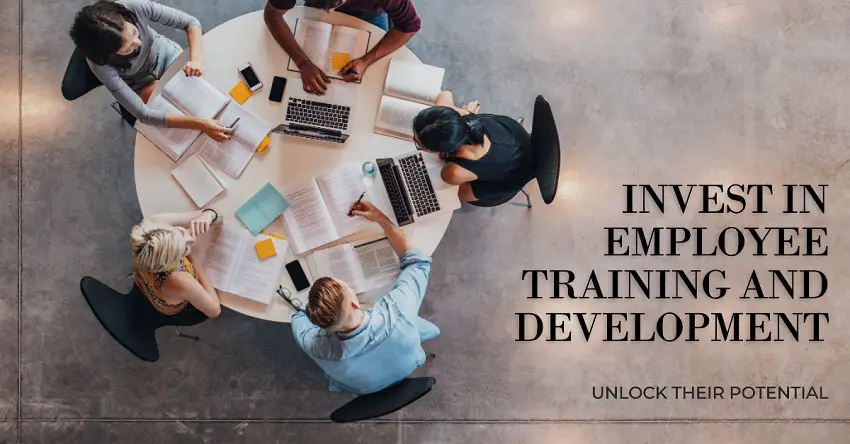
Equipping employees with the necessary skills and knowledge is crucial for enhancing operational efficiency. By investing in training and development programs the businesses can improve employee performance, increase productivity and reduce errors.
Identify specific training needs based on job requirements and performance gaps. Provide comprehensive training programs that address technical skills, process knowledge, and problem-solving abilities. Ongoing training ensures that employees stay up-to-date with industry advancements and are capable of performing their tasks efficiently.
Encourage a learning culture within the organization, where employees are motivated to enhance their skills and share knowledge. Promote cross-training initiatives to enhance flexibility and enable employees to perform multiple roles when necessary. By investing in employee development, businesses create a skilled workforce that contributes to operational efficiency and continuous improvement.
3. Adopt Technology Solutions
Leveraging technology solutions can significantly enhance operational efficiency. Automation, digital tools, and data-driven analytics provide opportunities to optimize processes, improve accuracy, and reduce manual errors. Identify areas where technology can streamline operations and reduce time-consuming tasks.
4. Foster Effective Communication and Collaboration
Effective communication and collaboration are essential for enhancing operational efficiency. Clear communication channels ensure that information flows seamlessly across departments, enabling timely decision-making and preventing costly delays.
Implement regular communication mechanisms such as team meetings, project updates, and cross-functional collaboration sessions. Encourage employees to share ideas, provide feedback, and communicate challenges they encounter in their workflows.
Collaboration tools and project management software facilitate efficient teamwork, task allocation, and progress tracking. By fostering a collaborative work environment, businesses can break down silos, improve coordination, and streamline processes, resulting in enhanced operational efficiency.
5. Continuously Measure and Improve Performance
Continuous measurement and improvement are fundamental to enhancing operational efficiency. Establish key performance indicators (KPIs) that align with organizational goals and regularly track performance against these metrics.
Monitor process metrics, such as cycle time, throughput, and defect rates, to identify areas for improvement. Analyze performance data and identify trends or patterns that indicate potential bottlenecks
Monitor and Reduce Energy Consumption
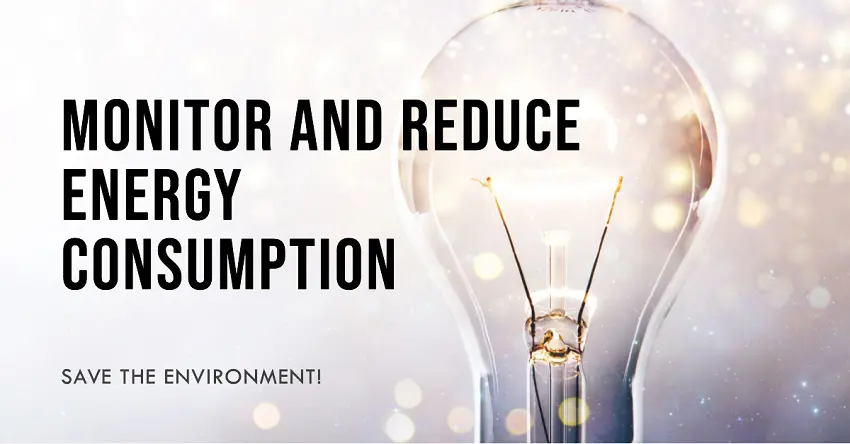
Reducing in energy consumption is beneficial for the environment and lead to substantial cost savings. By implementing effective strategies to monitor and control energy usage, organizations can optimize their operations while minimizing their environmental footprint. Here are some valuable tips
1. Conduct Energy Audits
Regular energy audits are a vital step in understanding and optimizing energy use. These audits involve assessing your current energy consumption patterns, identifying areas of inefficiency, and developing strategies for improvement. By analyzing utility bills, inspecting equipment, and evaluating lighting and HVAC systems, you can pinpoint areas where energy is being wasted and take measures.
2. Invest in Energy-Efficient Equipment
Outdated machinery and appliances are often energy hogs. By replacing them with energy-efficient alternatives, businesses can significantly lower their energy costs. Look for equipment that carries high energy-efficiency ratings, such as appliances labeled with the Energy Star logo. .
3. Implement Energy Management Systems
Energy management systems provide real-time data on energy usage, allowing you to identify patterns, optimize resource allocation and track progress. By leveraging energy management systems businesses can make informed decisions to reduce energy waste and improve overall efficiency.
4. Optimize Lighting and HVAC Systems
Lighting and HVAC systems are significant contributors to energy consumption. Upgrading lighting to energy-efficient LED bulbs can yield substantial savings as they consume less electricity and have a longer lifespan. Additionally, investing in programmable thermostats and smart HVAC controls allows for better temperature regulation, reducing energy waste while maintaining comfort levels.
Invest In Employee Training And Development
Encourage a learning culture within the organization, where employees are motivated to enhance their skills and share knowledge. Promote cross-training initiatives to enhance flexibility and enable employees to perform multiple roles when necessary. Businesses create a skilled workforce by investing in corporate gifting and employee development, contributing to operational efficiency and continuous improvement.
Minimize Waste and Implement Recycling Programs
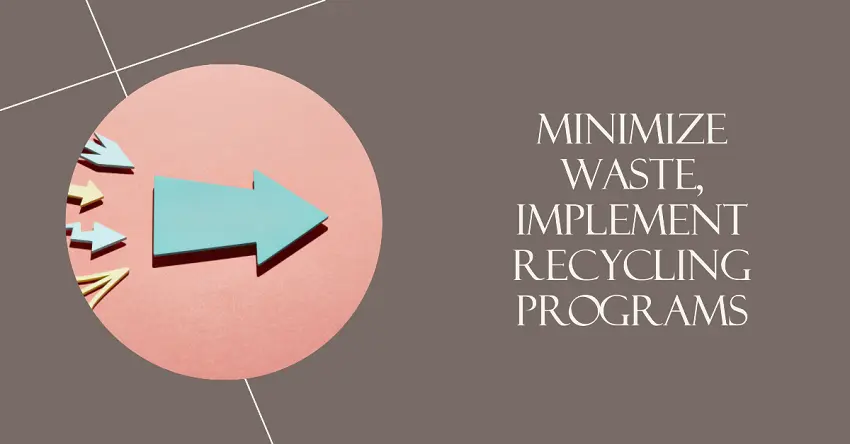
Minimizing waste and implementing effective recycling programs are essential for businesses aiming to reduce their environmental footprint and cut costs. By conducting waste audits, developing waste reduction plans, and incorporating recycling initiatives, organizations can make significant strides towards achieving sustainability goals. Here are key tips to help you minimize waste and implement recycling programs:
1. Conduct Waste Audits
Waste audits are valuable in identifying areas where resources can be reused or recycled, leading to reduced waste and lower costs. By assessing your current waste generation patterns, you can pinpoint opportunities for improvement. Analyze the types and quantities of waste produced, and identify areas where materials can be repurposed or eliminated.
2. Implement a Waste Reduction Plan:
Create a waste reduction plan tailored to your business’s specific needs. Streamline operations and eliminate unnecessary steps that contribute to waste generation. Engage employees in the process by raising awareness about waste reduction and empowering them to suggest ideas.
3. Incorporate Recycling
Implementing a recycling program is necessary for diverting waste from landfills and reducing disposal costs. Identify recyclable materials commonly generated in your business, such as paper, plastic, glass, and metals. Set up designated recycling bins throughout your facilities, clearly labeled for different materials. Educate employees about proper recycling practices, including sorting recyclables and ensuring contamination-free materials.
